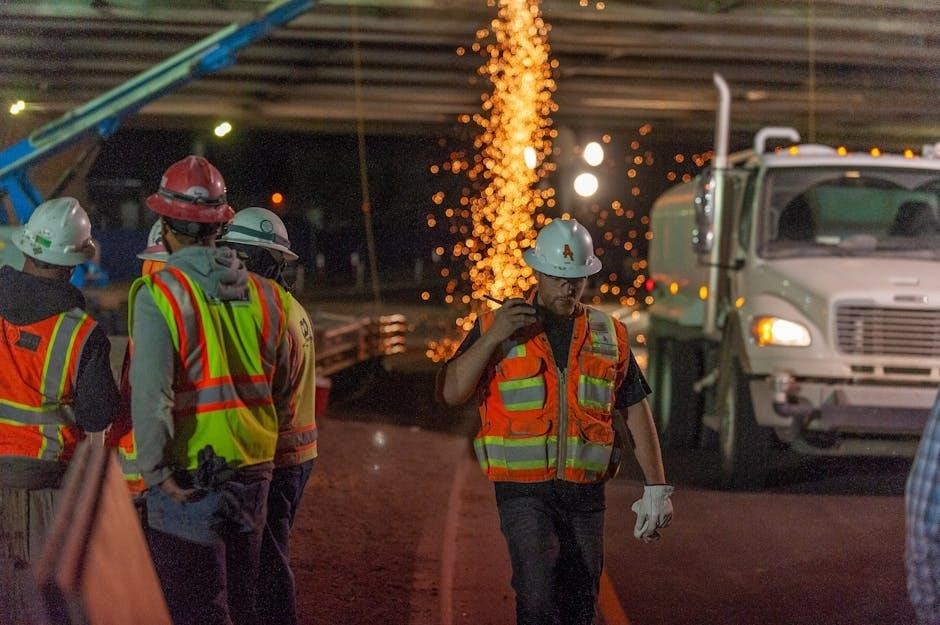
A well-structured semi truck preventive maintenance checklist is essential for ensuring safety, reliability, and peak performance of your fleet; Regular inspections help prevent breakdowns, reduce repair costs, and maintain compliance with regulations.
Importance of Preventive Maintenance for Semi Trucks
Preventive maintenance is critical for semi trucks to ensure safety, reliability, and optimal performance. Regular inspections help identify and address potential issues before they lead to costly breakdowns or accidents. By following a structured preventive maintenance checklist, fleets can reduce downtime, extend vehicle lifespan, and maintain compliance with regulations. This proactive approach also enhances driver safety and reduces the risk of unexpected repairs, ultimately saving time and resources. A well-maintained fleet not only improves operational efficiency but also contributes to customer satisfaction and business reputation.
Overview of the Semi Truck Preventive Maintenance Checklist
A comprehensive semi truck preventive maintenance checklist organizes essential tasks to ensure vehicle safety and efficiency. It typically covers daily, weekly, monthly, and annual inspections, addressing key systems like engines, brakes, tires, and electrical components. The checklist includes tasks such as fluid level checks, filter replacements, and inspections of belts, hoses, and lights. By following this structured approach, fleets can track maintenance progress, identify potential issues early, and comply with DOT regulations. Regular use of this checklist helps reduce unexpected breakdowns and extends the lifespan of the vehicle.
Daily Preventive Maintenance Checks
Daily checks ensure semi truck safety and performance. Include pre-trip and post-trip inspections, checking fluid levels, tires, brakes, lights, and belts to prevent breakdowns and ensure compliance with safety standards.
Pre-Trip Inspection Checklist
A thorough pre-trip inspection is critical for ensuring safety and compliance. Start by checking tires for proper pressure and tread depth, and inspect brakes for functionality. Verify that all lights and signals are operational, and ensure the trailer is securely connected. Examine fluid levels, including oil, coolant, and diesel exhaust fluid, and look for any signs of leaks. Check belts and hoses for wear, and test the battery and charging system. Finally, review the trailer for damage or issues. A detailed checklist helps drivers systematically cover all critical areas, reducing the risk of breakdowns and ensuring a safe journey. Always follow manufacturer guidelines and FMCSA regulations for inspections.
Post-Trip Inspection Checklist
After completing a trip, a detailed post-trip inspection is essential to identify potential issues before they escalate. Begin by inspecting the exterior for damage or dents, and check tires for signs of wear or damage. Look for fluid leaks under the truck and trailer, and ensure all connections are secure. Test brake systems for proper function and inspect air lines for damage. Review the instrument panel for warning lights, and check the trailer for proper loading and security. Document all findings and report any issues for timely repairs. This step ensures safety and prevents unexpected breakdowns. Always maintain detailed records for compliance and maintenance tracking.
Fluid Levels and Leaks
Checking fluid levels and inspecting for leaks is a critical part of semi-truck maintenance. Ensure engine oil, coolant, transmission fluid, and brake fluid levels are within recommended ranges. Look for signs of leaks around hoses, connections, and reservoirs. Addressing fluid issues promptly prevents engine damage, overheating, and brake failure. Use a preventive maintenance checklist to systematically inspect all fluid systems. Regular checks help avoid costly repairs and downtime, ensuring safe and efficient operation. Always refer to the manufacturer’s guidelines for specific fluid requirements and inspection procedures.
Belt and Hose Condition
Inspecting belts and hoses is vital to prevent unexpected failures. Check the serpentine belt for cracks, frays, and wear. Ensure proper tension to avoid slippage or breakage. Similarly, examine coolant, fuel, and air hoses for signs of degradation, leaks, or softening. Replace any damaged or aged components promptly. Regular checks help prevent overheating, engine damage, and costly repairs. Use a preventive maintenance checklist to monitor belt and hose condition, ensuring optimal performance and safety. Always follow manufacturer guidelines for inspection and replacement intervals to maintain fleet reliability.
Lighting and Electrical Systems
Inspecting the lighting and electrical systems ensures safety and compliance. Check all exterior lights, including headlights, brake lights, turn signals, and marker lights, for proper function and damage. Verify that emergency lights and hazard signals operate correctly. Inspect the electrical system for loose wires, corrosion, or damaged connectors. Test trailer connections to ensure proper communication between the truck and trailer. Use a preventive maintenance checklist to track these tasks. Regular checks help prevent safety hazards, electrical failures, and potential DOT violations. Maintain visibility and reliability on the road by addressing issues promptly.
Tire Pressure and Tread Depth
Correct tire pressure is critical for safety, fuel efficiency, and tire longevity. Use a pressure gauge to ensure tires are inflated to the manufacturer’s recommended levels, as underinflated tires can overheat and fail. Inspect tread depth using a tread depth gauge; minimum legal depth is 2/32 of an inch for steer tires and 1/32 for others. Uneven wear indicates misalignment or improper inflation. Addressing these issues prevents blowouts, improves traction, and ensures compliance with safety regulations. Regular checks help maintain optimal performance and reduce the risk of accidents; Include this in your preventive maintenance checklist for consistent monitoring.
Brake System Inspection
The brake system is critical for safety, requiring thorough inspection during preventive maintenance. Check brake pads for wear, ensuring they meet minimum thickness specifications. Inspect rotors for excessive wear or warping. Examine air lines and hoses for leaks or damage, and test the air pressure to ensure proper function. Verify that all brake lights and ABS sensors are operational. Lubricate brake components as needed to prevent corrosion and ensure smooth operation. Addressing issues promptly avoids costly repairs and enhances overall road safety. Include this in your preventive maintenance checklist for consistent monitoring.
Trailer Connection and Security
Ensuring a secure trailer connection is vital for safety and compliance; Inspect the tractor-trailer coupling for proper alignment and locking. Check tractor pins and kingpin for damage or wear. Verify air and electrical connections are clean and functioning correctly. Test trailer brakes to ensure synchronization with the tractor brakes. Lubricate the fifth wheel and kingpin to prevent rust and ensure smooth operation. Secure all tie-downs and ensure load distribution is balanced. Documenting these checks in your preventive maintenance checklist helps maintain a safe and efficient operation; Proper connection prevents accidents and delays, ensuring compliance with DOT regulations.
Battery Condition and Charging System
Regularly inspect the battery terminals for corrosion and secure connections. Check electrolyte levels and top off as needed. Test battery voltage and ensure proper charging. Inspect the alternator belt for wear and tension. Verify the charging system is functioning correctly. Look for signs of overcharging or undercharging. Clean terminals with a wire brush if necessary. Replace worn or damaged cables. Test battery health using a multimeter. Address any issues promptly to avoid unexpected power loss or system failures. A well-maintained battery and charging system ensures reliable engine startups and optimal performance.
Exhaust System Check
Inspect the exhaust system for leaks, damage, or rust. Check mufflers, pipes, and connections to ensure they are secure and functioning properly. Look for cracks or dents that could cause exhaust gas leaks. Verify the catalytic converter and diesel particulate filter are in good condition. Ensure all clamp connections are tight to prevent loose components. Address any issues promptly to avoid performance loss or emissions violations. A well-maintained exhaust system ensures reduced emissions, improved fuel efficiency, and compliance with environmental regulations.
Weekly Preventive Maintenance Tasks
Perform engine oil and filter checks, inspect air filters, and replace fuel filters. Check transmission fluid levels and ensure all grease fittings are properly lubricated for optimal performance and longevity.
Engine Oil and Filter Check
Regular engine oil and filter checks are critical for maintaining your semi truck’s performance and longevity. Always use the manufacturer-recommended oil grade and filter type. Check oil levels using the dipstick, ensuring it’s within the specified range. Look for signs of contamination or degradation, such as discoloration or particles. Replace the oil filter during every scheduled service to prevent debris from entering the engine. Proper lubrication reduces wear on moving parts and prevents overheating, ensuring your engine runs smoothly and efficiently. Keep a log of oil changes to stay on track with maintenance schedules.
Air Filter Inspection and Cleaning
Inspecting and cleaning the air filter is a crucial step in maintaining your semi truck’s engine performance. Check for dirt, dust, or debris that may restrict airflow. If the filter is dirty, clean it with compressed air or replace it if damaged. Refer to the manufacturer’s guidelines for the recommended cleaning method. A clean air filter ensures proper engine airflow, improving fuel efficiency, reducing emissions, and preventing premature wear on engine components. Regularly servicing the air filter helps maintain optimal engine function and reduces the risk of costly repairs down the road.
Fuel Filter Replacement
Replacing the fuel filter is a critical task in semi truck maintenance. A dirty or clogged filter can lead to poor engine performance, reduced fuel efficiency, and potential damage to the fuel system. Inspect the filter for debris or contamination and replace it according to the manufacturer’s recommendations, typically every 15,000 to 30,000 miles. Use a high-quality filter to ensure proper fuel flow and engine performance. Regular fuel filter replacement helps prevent costly repairs, maintains engine health, and keeps your truck running smoothly on the road.
Transmission Fluid Level Check
Checking the transmission fluid level is a vital part of weekly preventive maintenance. Low or degraded fluid can cause overheating, reduced performance, and potential damage to the transmission system. Locate the transmission dipstick, wipe it clean, and insert it to measure the fluid level. Ensure the level is within the manufacturer’s recommended range. If the fluid is dirty or discolored, consider replacing it. Always use the specified type of transmission fluid for your semi truck. Regular checks help maintain smooth gear shifts, prevent costly repairs, and extend the lifespan of the transmission system.
Grease Fittings and Lubrication
Proper lubrication of grease fittings is essential for maintaining the longevity and efficiency of your semi truck. Weekly, inspect and grease all accessible fittings, including steering components, suspension joints, and axle ends. Use a high-quality grease suitable for heavy-duty applications. Ensure grease is applied evenly and in the recommended quantities. Over-greasing can attract dirt and cause premature wear. Clean fittings before applying new grease to prevent contamination. Regular lubrication reduces friction, prevents corrosion, and ensures smooth operation of moving parts. Neglecting this step can lead to component failure and costly repairs down the road.
Wheel and Hub Inspection
Inspecting the wheel and hub is critical for ensuring safety and performance. Check for wear, damage, or rust on wheels and hubs. Verify that all lug nuts are tight and properly torqued. Look for signs of corrosion or excessive heat, which can indicate issues. Ensure hubs are properly lubricated and free from contaminants. Inspect the hub caps for damage and secure them tightly. Check wheel seals for leaks and ensure they are functioning correctly. Addressing these issues promptly prevents potential failures and ensures smooth operation of the semi truck.
Suspension and Steering System Check
Inspect the suspension and steering system for wear, damage, or misalignment. Check spring leaves, shackles, and bushings for signs of deterioration. Ensure all tie rods and drag links are secure and functioning properly. Look for excessive play in the steering gear or steering box. Verify the steering fluid level and check for leaks. Test the system for smooth operation and proper alignment. Addressing these issues ensures improved handling, safety, and reduces the risk of component failure during operation.
Fifth Wheel and Kingpin Lubrication
Regular lubrication of the fifth wheel and kingpin is crucial for smooth trailer connection and operation. Inspect the grease levels and ensure proper application. Check for wear on the kingpin and fifth wheel plate. Lubricate every 3 months or 30,000 miles, or as recommended by the manufacturer. Neglecting this can lead to excessive wear, noise, or even trailer detachment. Proper maintenance ensures safety, reduces friction, and prevents costly repairs. Always follow the checklist to maintain optimal functionality and compliance with DOT standards.
Monthly Preventive Maintenance Schedule
Inspect coolant, replace drive belts, and check brake pads and wheel bearings. Lubricate the fifth wheel and ensure all systems are functioning optimally for safety and performance.
Coolant Level and Condition
Regularly checking the coolant level ensures proper engine temperature regulation. Inspect for leaks, discoloration, or contamination. Replace the coolant every 150,000 miles for severe duty and 300,000 miles for normal duty to prevent engine damage. Always use the recommended coolant type to maintain optimal performance and avoid corrosion. Record the coolant condition in your maintenance log to track service intervals and comply with DOT regulations. Proper coolant maintenance is crucial for engine longevity and fleet reliability.
Drive Belt Replacement
Inspect drive belts for cracks, wear, or fraying. Replace them every 50,000 to 100,000 miles or as recommended by the manufacturer. Neglecting belt replacement can lead to engine failure and costly repairs. Always use the correct tools to avoid damaging the belt or pulleys during replacement. Proper tension is crucial to ensure optimal performance and prevent premature wear. Keep a spare belt on hand for emergencies. Regular belt inspections and timely replacements are vital for maintaining engine health and avoiding unexpected breakdowns during operation.
Brake Pad and Rotor Inspection
Inspect brake pads for wear, ensuring thickness meets safety standards. Check rotors for warping or excessive scoring. Replace pads and resurface rotors as needed. Lubricate hardware to prevent seizing. Always follow manufacturer guidelines for inspection intervals and replacement thresholds. Neglecting brake maintenance can lead to reduced stopping power, increased risk of accidents, and DOT violations. Regular inspections ensure optimal braking performance and compliance with safety regulations, protecting both drivers and cargo. Maintain detailed records of inspections and repairs for audit purposes.
Wheel Bearing Packing
Regular wheel bearing packing is critical for maintaining proper lubrication and preventing premature wear. Inspect bearings for grease degradation or contamination. Clean and repack bearings with high-quality grease every 30,000 to 50,000 miles or as recommended by the manufacturer. Ensure all components, including the hub and spindle, are free from debris. Properly torque wheels after servicing to avoid damage. Neglecting this step can lead to overheating, bearing failure, and costly repairs. Always document the service for compliance and maintenance tracking.
Frame and Undercarriage Inspection
The frame and undercarriage are critical for the structural integrity of a semi-truck. Regular inspection ensures safety and durability. Check the frame for rust, cracks, or damage. Inspect the undercarriage, including cross members and brackets, for wear or corrosion. Look for loose or missing bolts and fasteners, and tighten them as needed. Neglecting this can lead to breakdowns and accidents. Ensure all components are in good condition to maintain stability and control on the road, while also complying with DOT regulations.
Electrical System and Connector Check
The electrical system powers essential functions of a semi-truck, from lighting to communication systems. Regularly inspect wiring, connectors, and fuses for damage, corrosion, or wear. Ensure all connections are secure and tight. Check for short circuits or faulty components. Test lighting systems, including headlights, brake lights, and turn signals, to ensure proper function. Addressing issues promptly prevents electrical failures, which can lead to accidents or equipment malfunctions. A well-maintained electrical system ensures safety and compliance with regulations.
DOT Inspection Preparation
Preparing for a DOT inspection is critical to ensure compliance with federal safety regulations. Regularly review and update your preventive maintenance checklist to address key areas inspected during DOT checks, such as brakes, tires, lights, and trailer connections. Verify that all documentation, including maintenance records and inspection reports, is accurate and up-to-date. Pay special attention to the fifth wheel, kingpin, and trailer coupling to ensure proper security and alignment. Addressing these areas proactively helps avoid costly citations and ensures a smooth inspection process, maintaining safety and compliance on the road.
Annual Preventive Maintenance Requirements
Annual maintenance includes engine overhauls, transmission service, differential fluid replacement, and complete brake system overhauls. These tasks ensure optimal performance and compliance with regulatory standards.
Engine Overhaul and Tune-Up
An annual engine overhaul involves a thorough inspection and replacement of critical components like pistons, rings, and valves. This ensures optimal performance and prevents engine failure. A tune-up includes spark plug replacement, fuel injector cleaning, and ignition system checks. These steps maintain fuel efficiency and reduce emissions. Proper documentation of these tasks is essential for compliance and future maintenance planning.
Transmission Service
Regular transmission service is crucial for maintaining the smooth operation of your semi-truck. This includes fluid level checks, filter replacements, and torque converter inspections; These tasks help prevent issues like overheating and wear on critical components. By following the manufacturer’s guidelines, you can ensure the transmission runs efficiently, reducing the risk of costly repairs. Proper documentation of these services is essential for maintaining compliance and extending the lifespan of your vehicle. A well-maintained transmission ensures reliable performance and minimizes downtime.
Differential Fluid Replacement
Regular differential fluid replacement is vital for maintaining the health and efficiency of your semi-truck’s drivetrain. Over time, the fluid can degrade, losing its lubricating properties and leading to increased wear and overheating. Replacing the differential fluid according to the manufacturer’s schedule ensures smooth gear operation and prevents premature component failure. Clean fluid also helps extend the lifespan of the differential, reducing the risk of costly repairs. Always use the recommended fluid type and follow proper disposal procedures for used fluid. Regular replacements contribute to optimal performance and minimize downtime.
Complete Brake System Overhaul
A complete brake system overhaul is a critical part of semi-truck maintenance, ensuring safety and reliability. This process involves inspecting and replacing worn or damaged components such as brake pads, rotors, drums, chambers, and air hoses. Proper alignment of brake shoes and adjustment of the braking system are also essential. Regular overhauls prevent brake failure, which can lead to accidents and costly repairs. Always follow the manufacturer’s guidelines and comply with FMCSA regulations to ensure the overhaul meets safety standards. A well-maintained brake system is vital for protecting drivers, cargo, and other road users.
Trailer Maintenance and Inspection
Regular trailer maintenance and inspection are vital for ensuring safe and efficient operations. Inspect the trailer frame, crossmembers, and landing gear for damage or rust. Check braking systems, including air lines and chambers, for leaks or wear. Verify electrical connections and lighting systems are functioning properly. Tire condition, tread depth, and pressure should be monitored, along with wheel bearings and seals. Additionally, inspect the coupling devices, such as the fifth wheel and kingpin, for proper alignment and lubrication. Addressing issues promptly prevents breakdowns and ensures compliance with safety regulations, reducing risks during transit.
Wheel Alignment and Balancing
Proper wheel alignment and balancing are critical for optimal semi-truck performance and safety. Misaligned wheels can lead to uneven tire wear, reduced fuel efficiency, and increased operating costs. Tire balancing ensures smooth operation, minimizing vibrations that can cause driver fatigue and mechanical stress. During annual maintenance, inspect wheel alignment and balance, checking for wear on suspension components and axles. Use manufacturer-recommended tools and guidelines to ensure accuracy. Correcting alignment and balancing issues prevents long-term damage and enhances overall vehicle stability, contributing to safer and more efficient fleet operations.
Documentation and Compliance
Accurate documentation of maintenance activities ensures compliance with FMCSA regulations, avoiding potential penalties. Properly maintained service records also facilitate smooth inspections and demonstrate adherence to legal requirements.
Recording Maintenance Activities
Accurate and detailed documentation of all maintenance activities is crucial for compliance and accountability. Maintaining a record of each service, including dates, mileage, and tasks performed, ensures transparency and simplifies audits. This documentation also serves as proof of adherence to FMCSA regulations and manufacturer guidelines. By keeping a comprehensive log, fleet managers and drivers can track maintenance history, identify patterns, and plan future services effectively. Digital tools and checklists can streamline this process, ensuring data is organized and easily accessible for inspections or compliance reviews. Proper recording also aids in warranty claims and supports long-term fleet management strategies.
Compliance with FMCSA Regulations
Adhering to FMCSA regulations is critical for ensuring safety and avoiding penalties. A preventive maintenance checklist helps fleets comply by systematically addressing required inspections and maintenance tasks. Regular checks, such as pre-trip and post-trip inspections, align with FMCSA guidelines. Maintaining detailed records of these activities provides proof of compliance during audits. Proper documentation also ensures that all safety standards are met, reducing the risk of violations. By following a structured checklist, fleets can stay aligned with regulatory requirements, promoting safer operations and avoiding costly penalties. Compliance is not just a legal obligation but a cornerstone of responsible fleet management.
Maintaining Service Records
Accurate and detailed service records are vital for tracking preventive maintenance activities. A well-documented checklist ensures that all tasks are recorded, providing a clear history of servicing. This documentation helps in planning future maintenance, ensuring compliance with regulations, and verifying the condition of the vehicle. Proper record-keeping also aids in identifying potential issues early, reducing downtime and extending the lifespan of the truck. By maintaining organized and accessible records, fleets can improve efficiency, accountability, and overall maintenance management. Regular updates ensure that all services are accounted for, supporting seamless operations and audits.
A well-executed preventive maintenance checklist ensures safety, efficiency, and compliance. Regular inspections and timely repairs optimize fleet performance, reduce downtime, and enhance overall operational reliability.
Benefits of a Comprehensive Maintenance Checklist
A detailed semi truck preventive maintenance checklist offers numerous benefits, including enhanced safety, reduced downtime, and cost savings. It ensures all critical components are inspected regularly, minimizing unexpected breakdowns. A structured checklist improves organization, allowing fleets to track maintenance progress efficiently. By addressing minor issues early, it prevents major repairs and extends equipment lifespan. Additionally, it helps maintain compliance with regulations, avoiding potential fines. Overall, a comprehensive checklist is a vital tool for optimizing fleet performance, ensuring reliability, and promoting a culture of proactive maintenance.
Final Tips for Effective Preventive Maintenance
To maximize the effectiveness of your semi truck preventive maintenance checklist, always adhere to manufacturer-recommended schedules and tailor the checklist to your fleet’s specific needs. Regularly review and update the checklist to reflect changing conditions or new regulations. Encourage drivers and technicians to thoroughly document findings and promptly address any issues. Leveraging digital tools for checklist management can enhance efficiency and accountability. Finally, ensure all staff are trained on the importance of preventive maintenance and how to correctly use the checklist. Consistency and attention to detail are key to achieving long-term benefits.